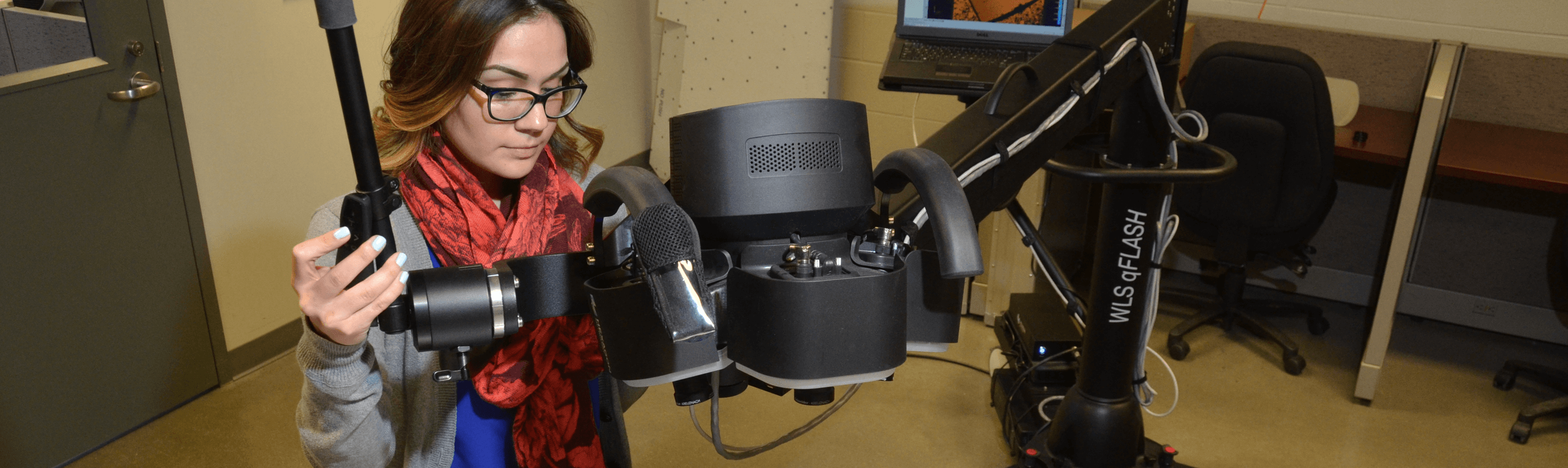
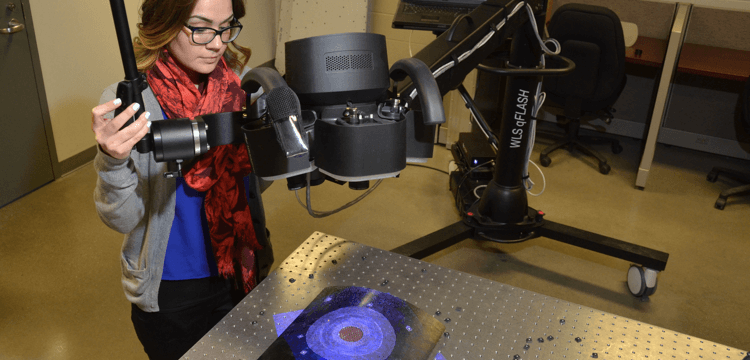
Spirit Patented Processes
Spirit AeroSystems not only employs the latest technology — the company originates it. Spirit develops unique intellectual property and technologies to improve customers’ products. Research and development is most focused on the architectural design of Spirit’s principal products: fuselages, propulsion and wing systems. The following proprietary processes and technologies are some of the many that have been developed by Spirit and are integrated into the production of those products.
Inflexion®
Spirit’s Inflexion technology eliminates the need for fasteners. Typically, composite structures are formed using rigid tools that must be removed from inside the product. This limits the complexity and size of the structures other manufacturers can produce. With Spirit’s Inflexion technology, tooling can transform between rigid and flexible states during the manufacturing process. This allows Spirit to build large, complex composite aerostructures to be designed and built for you in one continuous piece, resulting in products that are lighter, more affordable and more efficient.
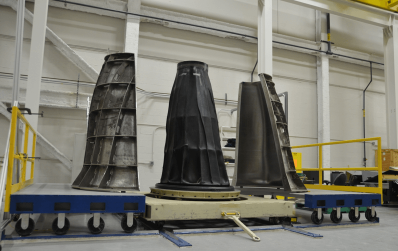
Spirit Exact®
Spirit Exact is a suite of technologies that enables parts to become tools, improving quality and drastically reducing the cost of tooling. Spirit Exact minimizes or eliminates the need for part-locating tools, thereby increasing quality and reducing costs. Spirit Exact can streamline the design and manufacturing of both metal and composite products.
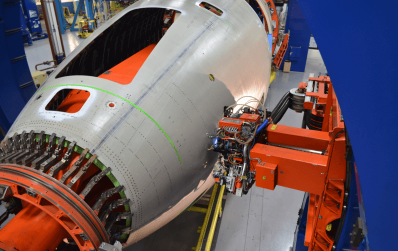
IRIS™
Spirit’s Intelligent Resin Infusion System (IRIS) revolutionizes composite wing structures. IRIS is a proprietary processing system for the manufacture of complex integrated composite aerostructures. The process allows for self-heated tooling for greater process control, reduced cycle time and lower energy consumption. IRIS has the potential to reduce manufacturing costs by as much as 20 percent, a savings passed on to OEMs.
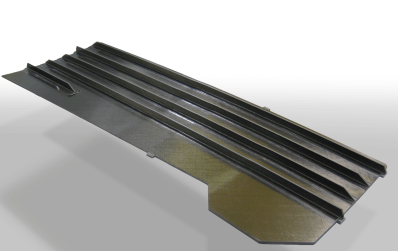
Resin Transfer Infusion (RTI)
The primary structural components of the A220 composite wing are manufactured using the patented RTI process. RTI uses ‘dry’ fabrics to create the structure and then resin is injected into the structure while it is in an autoclave. The process allows for the manufacture of large, one-piece complex structures, reducing the need for many different parts and mechanical fasteners. The process offers significant material savings and delivers reduced cycle times. The benefits to the customer include reduced inspection and maintenance activities, due to the corrosion-free properties of the materials, and significant weight reduction compared to a conventional metal wing.
Alloys
Spirit has developed a patent-pending alloy that combines the weight and cost benefits of aluminum with the temperature resistance found in more expensive materials like titanium.
Joule Form™
To minimize the cost and quality challenges associated with titanium forging and machining, Spirit developed Joule Form process. This capability enables Spirit to minimize waste and maximize value, while directing energy only where it is needed, thereby decreasing the cost of machined parts and minimizing the company’s carbon footprint.
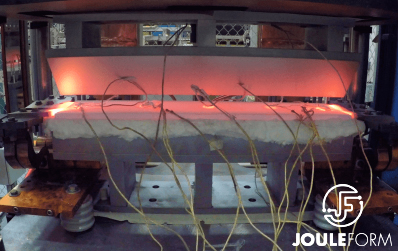
Non-Destructive Inspection (NDI)
Spirit leads the way in NDI capabilities. The company is constantly developing solutions to meet complex inspection challenges. Traditionally, composite stiffeners were inspected from the outside in, using off-the-shelf NDI equipment. But advanced, new composite designs are too complex to be inspected in the traditional way. Spirit’s research and development team developed a patent-pending technology that enables complex integrated structures to be inspected from the inside out.
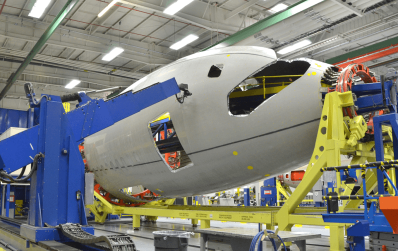
Explore More
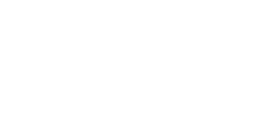