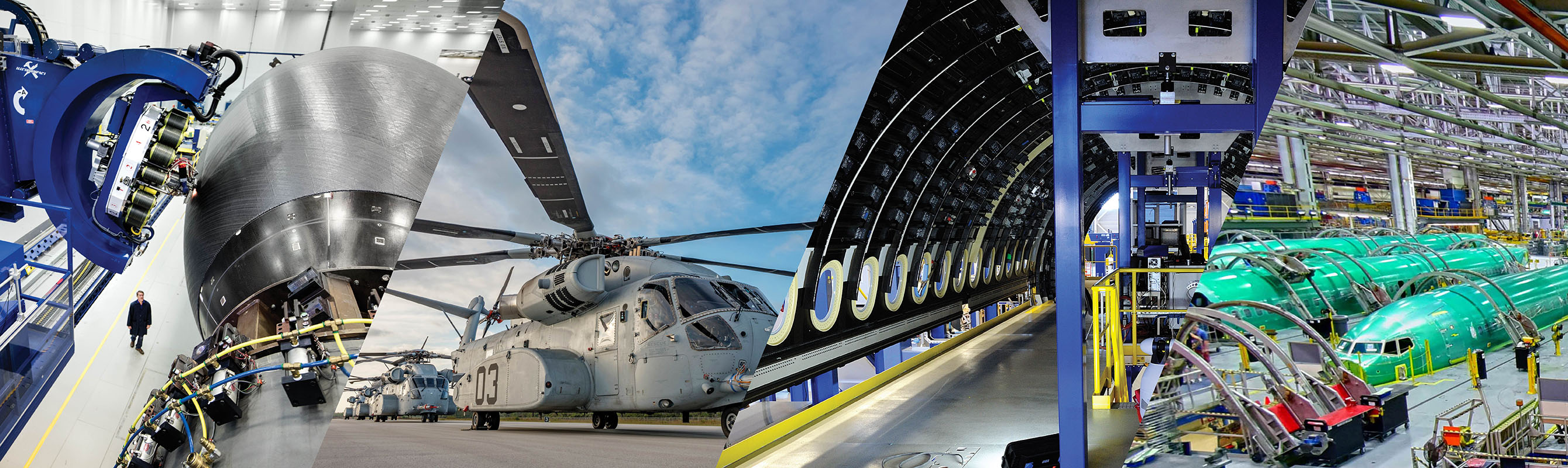
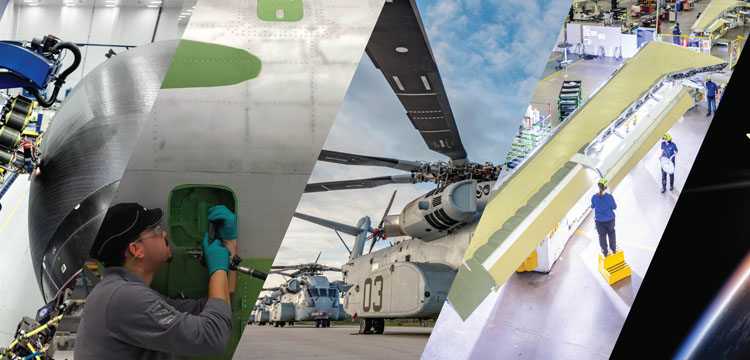
Connecting people, one click at a time
How Spirit One opens doors for new collaborations
Most aerospace manufacturers will tell you that when it comes to large programs, the devil is in the details. Each team member, part, and machine across the manufacturing design and production process needs to be orchestrated in sync to efficiently construct a quality product. When that doesn’t happen, it means more than lost productivity. It means a disconnect. It means both people and processes are not working as well as they could. This isn’t a challenge unique to one company or even to aviation. But we’ve been working on a solution – a transformative one that is equal parts design and build that will alter the way Spirit approaches future aviation programs.
Enter in Spirit One.
This digital transformation system is vital for keeping programs competitive. It isn’t a quick-fix for an ailing system; it is the result of carefully planned change. That’s why we’ve created Spirit One; an architecture that supports a single digital thread, with the capability to create a digital twin. Our goal is to boost efficiency and keep our cross-functional teams connected with a single source of data that connects people and addresses program needs in real-time. Ultimately, Spirit One improves our ability to industrialize and drives down manufacturing costs, thus elevating program development beyond industry norms.
Digital twinning and the digital thread
When it comes to manufacturing challenges, digital twinning is winning. Twinning incorporates information across all steps in the conception, design, fabrication, and production processes. One platform that provides digital twin capability is 3DXperience. This is done through a three-dimensional modeling software called 3DX, CATIA V6. Twinning is an incredibly valuable shadow to the physical world:
- Information is shared in real-time with OEM suppliers and internal team members.
- Engineers can simulate in the virtual world and make changes to a piece of equipment or part without disrupting fabrication or assembly.
- Simulations can be performed at any point in the process, cutting down on hiccups or interruptions.
The beauty of the digital thread is that it connects design, fabrication, and the supply chain in one seamless architecture. Every part of the manufacturing process talks to one another. This gets at the most important part of this system: connecting people and process.
When the two aren’t connected, frontline managers do not have the information they need to make immediate decisions impacting their process. For example, they might be chasing down a part they no longer need, while a piece of equipment that costs tens of millions of dollars is sitting idle. It results in lost time, delaying the build on an expensive piece of equipment for an issue that’s preventable.
With Spirit One, multiple teams, from those in Design, fabrication to those in production, can look at the same set of data, while working synchronously. This enables everyone to see exactly where parts, processes, and projects are tracking. The digital thread significantly enhances our collaborative integrated product teams, keeping projects moving quickly and efficiently. Each person can apply their unique perspective to the same set of information everyone else has. It means all the people working on a single program can make more informed, high-value decisions.
Digital transformation in action
While the industry has seen brutal impacts over the past year, Spirit has continued our investment in research and technology to move our digital transformation forward. We have not shied away from embracing new technologies to help improve processes and keep our employees focused where they’re needed across the supply chain. As such, digital transformation capabilities are already in use in several Spirit facilities:
- Global Digital Logistics Center (GDLC). With the capacity to hold over 120,000 parts, this 45,000 square foot aviation warehouse is the largest of its kind. The massive inventory is managed by a single automated storage and retrieval system (ASRS) that works in tandem with an advanced warehouse control system. By capitalizing on these digital systems, the ASRS makes it easy to store and organize thousands of parts. Less than a year after opening, the GDLC is already operating with 99.97% delivery accuracy.
- Digitally Re-Engineered Spoilers. Focused specifically on the Airbus A320 family spoiler, our Prestwick facility utilizes advanced composite technology in the development of new materials. Spirit’s integrated product teams used a suite of digital tools, as well as a newly created production system, to redesign these spoilers from a sandwich core configuration to a monolithic RTM product. Equipment suppliers were also integrated with the team to support quick-iteration trade studies on factory and cost impacts due to evolving design and process changes. The entire facility was simulated and optimized – including an AR walk-through – before concrete was cut or equipment installed. A manufacturing execution system orchestrates every operation of the build process and ensures the pace of the flow is meeting production demand. As a result of this work, Spirit can service 700 aircraft and 7,000 spoilers annually at this facility, while also creating over 100 new jobs.
- Automated Floor Beam Assembly. Manual floor beam assembly used to take place in several stations of our Wichita facility. For the forty-seven 737 MAX-8 floor beams, there are more than 400 different configurations. To automate their assembly, our technical teams created a process and digital twin of the tooling and equipment plan that allowed the new process to be perfected digitally before developing the actual tooling and equipment. By working digitally, the team was able to build a successful system that cuts down on assembly time. .Digital transformation brings quality work to market faster, which saves costs in the long run. These benefits prove how digital transformation can improve manufacturing processes of all scopes.
The future of manufacturing
The days where separate teams only worked within small sections of a project are disappearing. Thanks to digital transformation programs like Spirit One, connected teams will lead the way into the future of aviation. But even though Spirit One is changing manufacturing processes for the better, one thing won’t change: the passion of the people behind the data. Digital transformation takes that passion for the work and streamlines it, making it even easier to stay connected. As a result, people are reinvigorated, supply chains are efficient, and the industry is poised for continued success.
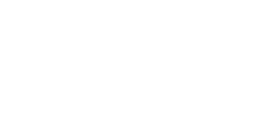