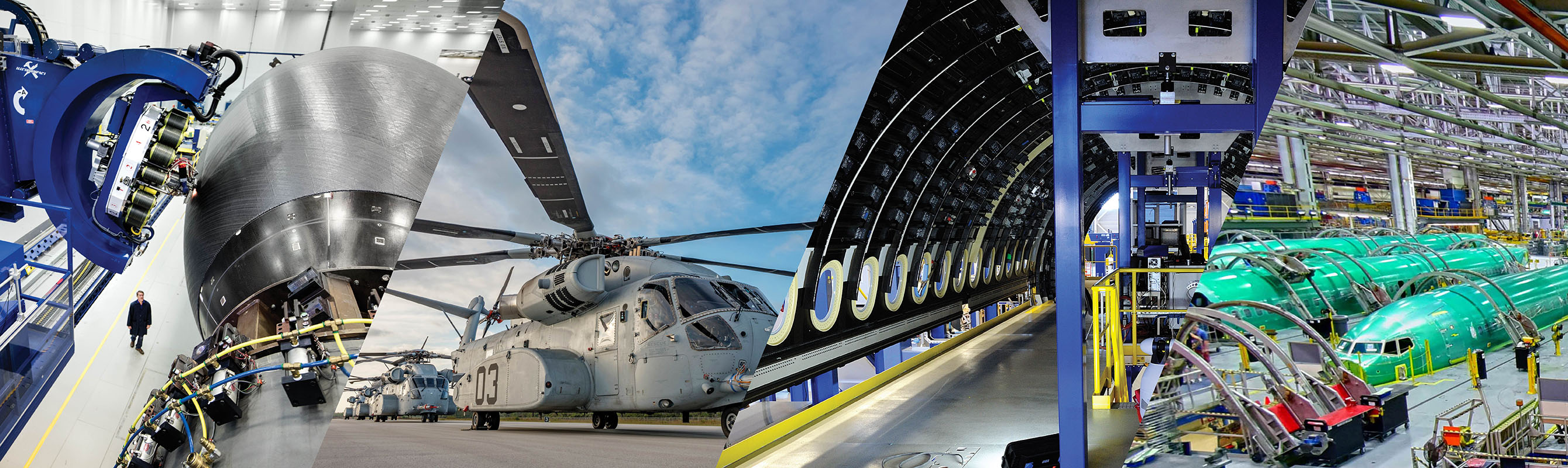
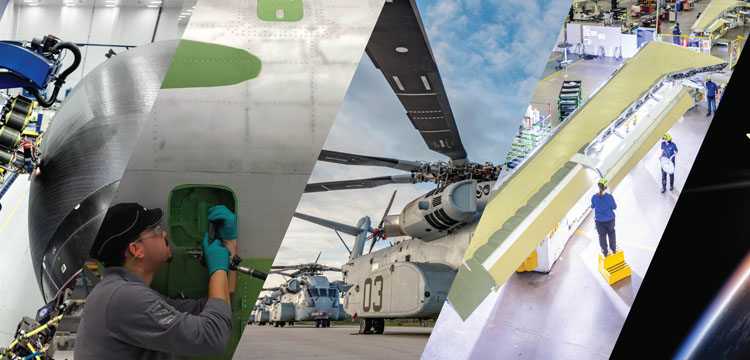
Building Better and Lighter: How Thermoplastic Composites Will Accelerate the Future of Aviation
When you look at an aircraft, what do you see? They are time capsules, holding within them the latest, greatest ideas of their generations. So, when we look to the future of flight, what do we want the next generation of aircraft to show about our time? We want to show that they are lighter. Faster. And more sustainable. The use of advanced, structural thermoplastic composites is one solution to bring us there. But lack of proper equipment, space and focus have kept them from being utilized to their full potential across the industry.
Development of next-generation fabrication processes, like automated forming, material placement and welding, must be industrialized to make thermoplastics commonplace in large-scale aerospace manufacturing. Spirit is driving towards that goal, bringing thermoplastic composites to new markets like eVTOL and attritable aircraft while laying the groundwork for conventional thermoplastic aerostructures.
Why are thermoplastic composites important in aerospace?
Traditional metals like aluminum and steel make up 70% of aircraft in circulation. But demands for lighter, more efficient aircraft are rising. We have substantial expertise with thermoset composites for reducing weight of aircraft, but our focus is expanding to include thermoplastic composites in production as well. Both material types use high-specific stiffness and strength of carbon fiber reinforced polymers to design lighter and stronger aircraft.
Currently, thermoplastics are replacing traditional materials in a variety of applications and are generally utilized for smaller parts. But using thermoplastics in larger components, like stringers, frames, bulkheads, and fuselage skin panels, can be incredibly beneficial. We aim to utilize thermoplastic composites in applications where automated high-rate manufacturing is possible. This means repeatedly melting, forming and solidifying material in very short cycle times.
How will thermoplastic composites support the next generation of aircraft?
We’ve identified three key areas where thermoplastics can be best utilized: the next generation of conventional aircraft, attritable aircraft, and emerging markets like urban air mobility (UAM). Each area requires lightweight, high-performance aircraft, with components that are affordable, easily produced and incredibly durable.
- Conventional aircraft. The next-generation fleet of conventional aircraft needs to prioritize reducing emissions and saving fuel costs, as well as manufacturing costs. A material that saves weight, is more affordable, is recyclable, and retains quality is needed.
- Attritable aircraft. Attritable aircraft, a strategic development focus within defense, are unmanned and intended to support manned craft that can venture into locations we wouldn’t want to send people. We need production to be cost-effective so we’re able to sacrifice them while saving pilots’ lives, without feeling a great loss in budget.
- Emerging markets like UAM. Some emerging markets, like UAM, are going to look a lot different in the way we manufacture and produce aircraft today. Thermoplastics can help produce these aircraft quickly and on a rolling basis.
How thermoplastic composites capability can meet program needs
Marrying capabilities to meet program needs takes years of development. Mastering the expertise required for these complex processes is a challenge felt by the entire industry. But we’ve prioritized process improvement in this area. Through research and development, we are finding creative ways to make thermoplastics a more commonly used material.
Our efforts aren’t stopping there. We are continuing to develop additional thermoplastic capability for implementation in the near future. Some of these capabilities include:
- Automated fiber placement (AFP). As the largest user of automated fiber placement machines in the world, we are applying this capability for high-rate layup of thermoplastic tows. This highly efficient fabrication method reduces cost and enables manufacture of largescale, weight-efficient structures. Our recently acquired thermoplastic automated fiber placement head is the first of its kind and a demonstration of how we are leveraging our technical expertise to further our thermoplastic capabilities.
- Induction welding of thermoplastics uses a coil and a high frequency alternating magnetic field to induce eddy currents in conductive reinforcement to generate heat. With this process, thermoplastic parts are fused together under pressure, yielding a cohesive assembly without additional materials, like adhesives in the bondline. This technology reduces aircraft weight by joining parts without fasteners and allows for a much faster production rate for component assembly. We recently showcased a Nose Wheel Well Bulkhead assembly at the 2020 American Composite Manufacturers Association (ACMA) Thermoplastic Composite Conference, which demonstrated thermoplastic AFP of large and complex geometry, and assembly with Spirit’s proprietary induction and resistance welding technologies.
- Large Scale Complex Forming. To take advantage of high-rate welding, components must be compatible thermoplastics. We are pushing the limits of scale and complexity for traditional thermoplastic stamp forming and exploring alternative methods for forming high-aspect ratio parts with variable cross sections. One example of a complex stamp formed part we are developing is fuselage frame segment which has ply drops and tow steering.
Today’s aircraft have legacy written throughout their bodies. Every machine, from military helicopters to commercial jets, have been born of the greatest minds in the industry. And thanks to innovations like thermoplastics, today’s aircraft are changing their forms to be better and lighter than ever before. But the story of thermoplastics in aerospace is just beginning. Refined processes are needed to make these materials commonplace in aerospace manufacturing. The time is now to prioritize thermoplastics development and allow the newest generation of ideas to take flight.
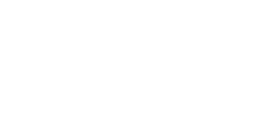